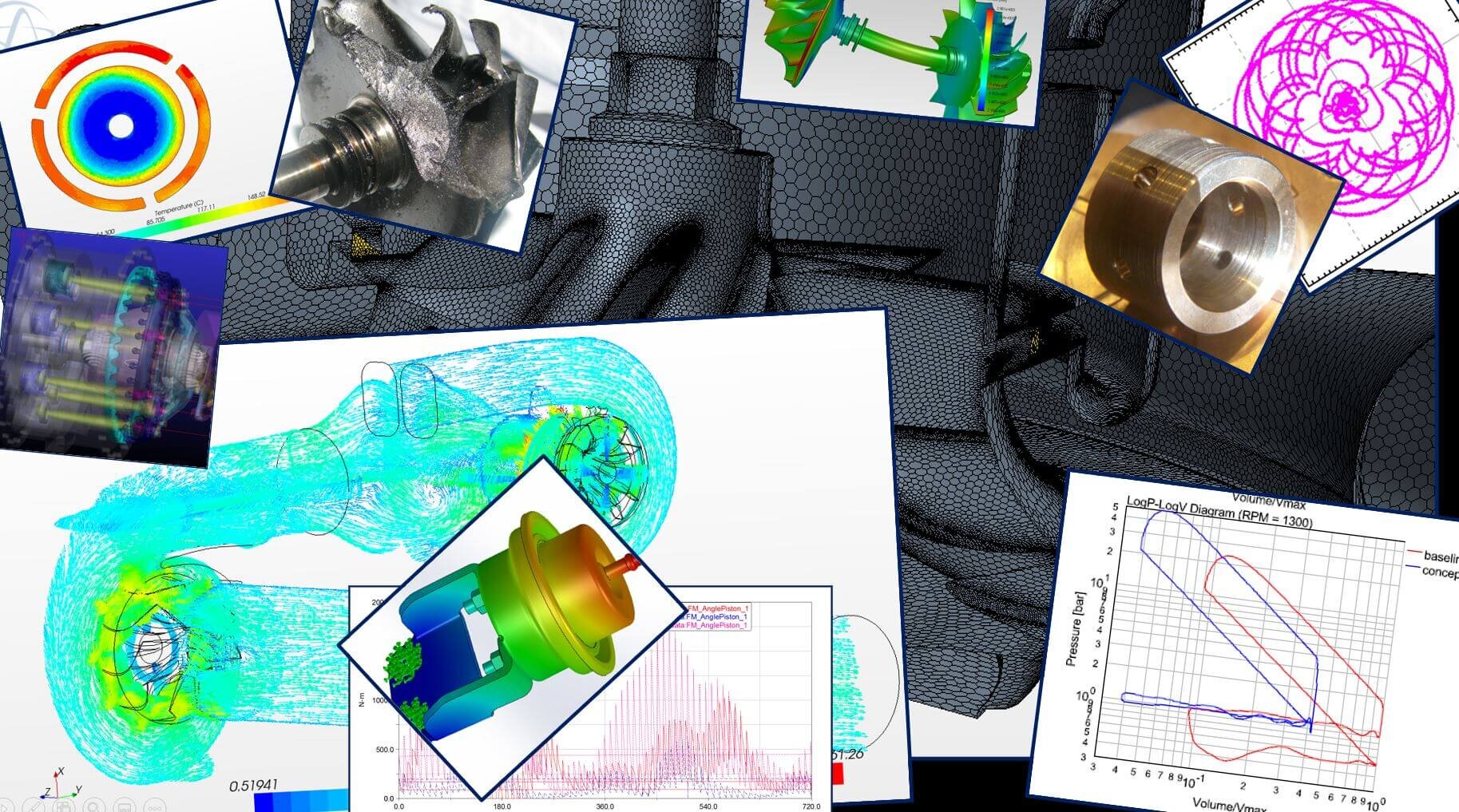
We can work with you to solve current production problems or develop and refine ideas into production-ready products. Our consulting and analysis areas of expertise include:
Retained Consulting
Over the past 11 years, retained consulting has been our most popular consulting arrangement. With retained consulting, the client pays a monthly fee. That empowers the client to tap into Steve’s 35 years of experience and ask questions and request analyses, design or research. We respond as close to immediately as possible; it becomes our #1 priority. You have questions and need answers NOW, not tomorrow or next week. As we have clients all over the world, we try to be available 24/7/365. What is important for the client is answers, not hours spent. For clients that use retained consulting, they only have to get internal approval once, not every time a question comes up. We are flexible as this arrangement only works when both parties feel they are getting value from the relationship and their investment. The monthly fee is based on an approximate amount of work over a long time period. If the arrangement is not working to everyone’s satisfaction, we adjust.
Complete Turbocharger Design
We have the capability to design state-of-the-art turbochargers—including higher efficiency compressors and turbines and/or more reliable turbochargers. There is still low-hanging fruit in today’s turbos to improve aerodynamics and bearing systems.
Multi-stage units are also in our wheelhouse as we have done both multi-stage compressors, and multi-stage turbines.
Aerodynamics and CFD Analysis
Our CFD models typically include all of the intricate details of the design—we do not simplify for aero analysis as we use the detailed CAD models along with automated meshing. If there is a threaded hole opening up into the volute, it’s in the real world and it’s in the model.
As another example, there is leakage through the compressor seal, and a complex pressure field behind the compressor. How the wheel hub line aligns with the center housing or seal plate pocket has a big impact on the flow field behind the compressor. That flow field has a lot to do with compressor oil seal leak characteristics. It can also be used in the calculating the net force on the wheel for thrust force calculations. Why just model the aero performance when you can provide data for the design of seals or thrust bearings?
Solve Difficult Problems
Forensic analysis is difficult on a turbocharger as the turbo has a lot of different functions going on in a very small package. Turbos also operate at extreme speeds (and temperatures) and when something goes wrong, the secondary damage after the primary failure usually clouds the issue. Finding the root cause is critical to solving the problem. Often engineers jump to solutions before the root cause is identified. Steve has decades of experience analyzing failed hardware, identifying the root cause, and then finding a solution which eliminates the problem. Let us find the root cause and fix your next thorny issue.
Engine Matching
Our internal software allows us to match engines much more quickly than engine simulation programs and without maps. It also allows us to look at the total system with advanced boosting systems and compare one vs another. Multiple turbos, multiple superchargers, HPL or LPL EGR, multiple inter-coolers, turbo-compounding, electric assist/compound, VGT, WGT. We can also handle two-stroke engine matching and low pressure natural gas engines. And of course, altitude.
Bearing Systems and Rotordynamics
We are experts in rotordynamics analysis and bearing system qualification, including shaft motion testing. We understand the linkage of key parameters such as the bearing stiffness and damping of the inner film and outer film to shaft motion performance including the impact of bearing speed on fully floating bearings. Every design we have done has passed shaft motion qualification on the first run. We also have designed a supercritical bearing system for electric assist turbochargers with a very large motor rotor. This also performed flawlessly on the first set of tests. You don’t have a viable turbo until you have a stable rotor bearing system!
Multi-stage Compressors and Turbines
We have also done multi-stage turbines and multi-stage compressors, including the inter-stage duct, outlet and inlet ducts. This type of problem has 5 frames of reference. We have had excellent correlation with subsequent testing.
We also understand the complex thermal field that is created by multiple stages and how to compensate so the thermal field doesn’t turn into a complex stress field and cause thermal cracking.
Variable Geometry Turbines
We have more experience than anyone on the development of variable geometry turbines, Steve has designed many different types of variable geometry, including 5 generations of multi-vane VGT, types with multiple volutes and switching valves, and the latest, the Variable Volute Turbine (VVT), patented by ESI.
VGTs are one of the most difficult pieces of hardware to design and validate. They operate at high temperatures where the mechanism glows red, but must move billions of times with little wear in spite of having no lubrication. The parts try to weld together, oxidize, sulfidize, and lose hardness through annealing. The vibration of the turbocharger may be 10g which adds to the wear, along with aerodynamic pulses each time a cylinder fires and opens the exhaust valve. If that is not enough of a challenge, the VGT is under a constantly changing thermal stress field as the power output of the engine changes with operator demand.
But we have done this many times and understand the failure modes and contributing factors—this is one of our core competencies.